For you and for us, things like used plating solutions, filters, and resins represent valuable materials to recover. To the U.S. EPA and DOT, they constitute hazardous waste, or at least regulated recyclable materials. And all hazardous waste generators, from jewelers to electronics manufacturers, bear full responsibility for its storage and transportation. But when it comes to shipping hazardous waste, many businesses still get a few things wrong.
While EPA regulates onsite hazardous wastes under RCRA, DOT regulates hazardous waste transportation. DOT requires that hazardous waste be classified, described, packaged, marked, labeled, and in condition for shipment according to its guidelines. When you ship materials to a refiner, failing to meet DOT requirements can result in hefty fines, reducing any revenue you generate through precious metal recovery.
By familiarizing yourself with these regulations, you’ll be better equipped to stay within the legal boundaries for shipping hazardous waste. You can also make better choices
for your business, including the companies you partner with for shipping and refining—decisions that can ultimately affect your bottom line.
To help you navigate the regulations and meet DOT shipping requirements, we’ve created the five-step checklist below. Note that steps 3, 4, and 5 include a few of the most common
mistakes we see shippers make.
1. Determine Whether Your Material is Hazardous Waste
DOT defines hazardous waste in 49 CFR part 171.8 as “any material that is subject to the Hazardous Waste Manifest Requirements of the U.S. Environmental Protection Agency specified in 40 CFR part 262.” This means that DOT considers your materials to be hazardous waste only if they must be shipped on a manifest under the federal RCRA waste requirements.
To determine whether your material falls under those requirements, answer these questions:
- Is it a solid waste, according to the EPA definition?
- Is it excluded from regulation under 40 CFR part 261.4?
- Does it meet any of the descriptions under the list of hazardous wastes in subpart D of 40 CFR part 261?
Thanks to an exemption in subpart F of 40 CFR part 266, recyclable materials from which “economically significant” amounts of precious metals are recovered are exempt from
full hazardous waste regulation. For your materials to qualify, you must receive an economic return valuable enough to cover the costs of recycling. However, you still have to comply
with all of the shipping requirements listed below, in addition to EPA’s record-keeping requirements.
2. Obtain an EPA ID Number (if you don’t already have one)
The EPA hazardous waste generator identification number allows EPA to track hazardous waste from cradle to grave. Whether or not you need an EPA ID number depends on
how much hazardous waste you generate per month, which determines your hazardous waste generator category.
If you generate more than 1,000 kg (2,200 lbs) per month, you are classified as a Large Quantity Generator (LQG) and you must obtain an EPA ID number.
If you’re a Small Quantity Generator (SQG), EPA does not require an ID number, but your state might, so it’s always best to also know the state-specific requirements.
You can find instructions and forms for obtaining an EPA ID number here.
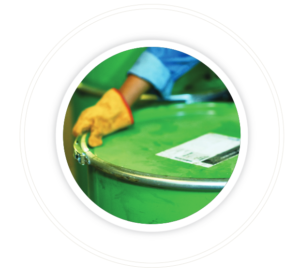
3. Fill Out the Hazardous Waste Manifest
The Uniform Hazardous Waste Manifest is designed to meet both EPA and DOT documentation requirements for shipping hazardous waste. It contains information
about the hazardous materials being transported (classification, reportable quantity, etc.), emergency contact information, the generator’s EPA ID number, and more. If you’re not tired of reading regulatory documents yet, you can find manifest requirements and instructions in Subpart C of 49 CFR part 172.
Fortunately, EPA rolled out the Hazardous Waste E-Manifest System in 2018 to replace its previously paper-intensive process. You can learn more about how the system works at the
EPA website and create an e-manifest using the RCRAInfo site.
Keep in mind, DOT still requires that transporters carry paper copies of the manifest. If you use the e-manifest system, simply print out a copy from the RCRAInfo site. (DOT recognizes electronic signatures specifically for e-manifests.)
Common Mistakes
One of the most frequently cited paperwork violations is a failure to properly describe the hazardous material. Be sure to consult the Hazardous Materials Table for proper shipping
descriptions and classifications, along with guidance for packaging and handling requirements.
For us, the most common mistakes we see on manifests are pretty simple:
- A shipper forgets to sign the manifest. Happens more than you think!
- The manifest has the wrong package count, in which case you’ll get a call from us to resolve it.
- The manifest shows an incorrect quantity of materials in a package, such as how much of a drum is full.
4. Choose the Right Packaging
General requirements for hazardous waste shipments and packaging are covered in 49 CFR 171.2(g) and 49 CFR part 173. DOT also offers a fairly easy to read summary here.
The Hazardous Materials Table in section 3 specifies the type of packaging required for each form of hazardous waste. For some materials, such as lithium cells and batteries, you may be required to use UN performance packaging.
If that’s the case, check out this guide to performance packaging from the Pipeline and Hazardous Materials Safety Administration (PHMSA). This two-page pdf shows you how to interpret codes and markings and includes a convenient list of volume conversion factors.
Common Mistakes
One of the most common shipping mistakes we’ve seen companies make is putting their material in improper packaging. That could mean using a poly drum when a steel drum
is required, or (this one makes us scratch our heads) putting liquids in a cardboard box instead of a drum.

5. Mark & Label Your Packages
This step provides crucial information for transporters, including orientation arrows, the nature of the waste (corrosive, flammable liquid or solid, etc.), shipper’s contact info and ID
number, hazardous material class, and more. DOT requirements for markings are listed in Subpart D of 49 CFR part 172, while labeling requirements are in Subpart E. PHMSA
also provides a handy markings, labeling, and placarding guide with general guidelines and visual examples.
While it’s important to follow the letter of the law when it comes to labeling, use some common sense, too. For instance, labels should be placed in a clear and visible
location on packages—that way, if an emergency response crew needs to get the information contained on a label, it’s quick and easy to find. Likewise, any
markings should be durable, in English, and not obscured by other markings
or labels.
Common Mistakes
There’s just one labeling mistake we see the most often: someone puts the wrong label on the wrong drum. It might seem like a minor slip-up, but the purpose of these labels is to communicate crucial information to everyone who handles your hazardous waste.
One Last Common Mistake
Here’s a word of advice that comes from years of fielding panicked calls from customers: Pay attention to the storage deadline for hazardous waste. EPA puts a limit on how much
hazardous waste you can accumulate onsite before it must be transported to a certified disposal facility. And, as you already know, shipping is hard to arrange at the last minute.
SQGs are allowed to store hazardous waste onsite for 180 days, according to 40 CFR section 262.16, while LQGs are limited to 90 days, per 40 CFR section 262.17. However,
if it’s day 89 and you suddenly realize you need to get the hazardous waste off-site tomorrow, you may not be able to find a shipping company with a suitable truck in the
area. So, we recommend you plan ahead and prearrange shipping, based on your expected hazardous waste accumulation.
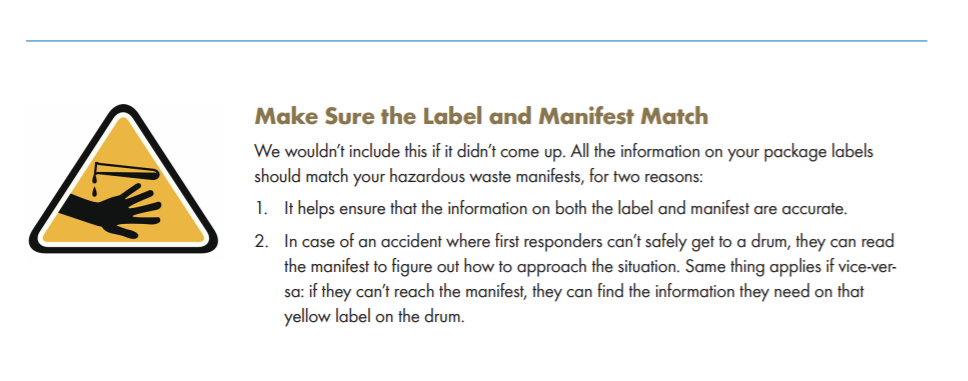